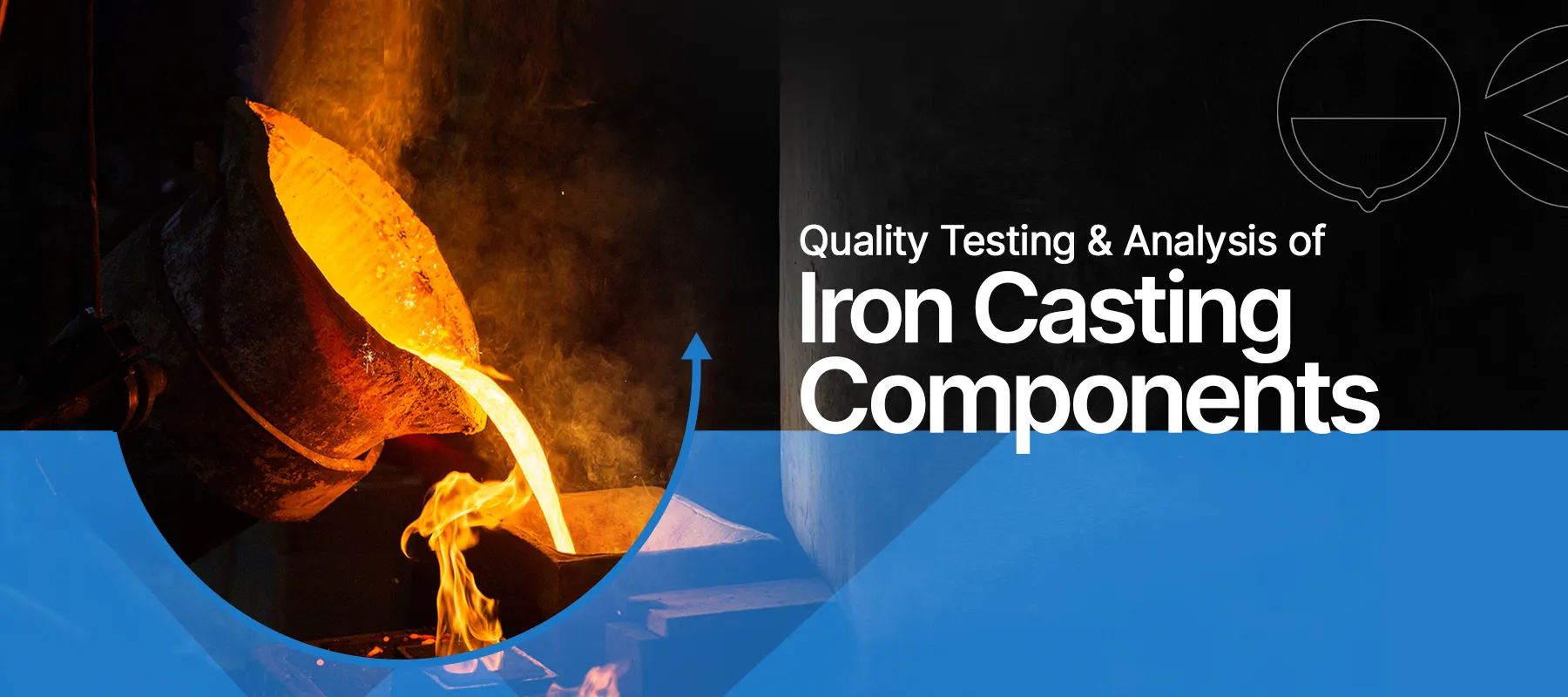
Quality Testing and Analysis of Iron Casting Components
Quality is paramount in the production of casting components. Rigorous and detailed post-production quality testing ensures that the end products delivered to customers are of the highest quality and accuracy. This commitment to quality sets top manufacturers apart, guaranteeing that every component meets and exceeds industry standards and customer expectations. Quality assurance in iron casting involves meticulous attention to detail at every stage of production, from raw material selection to final inspection. Implementing comprehensive testing protocols helps manufacturers identify and address potential issues before products reach the market, reducing failure risks and increasing customer satisfaction, while fostering long-term client relationships and trust.
Comprehensive Quality Testing Methods for Iron Castings
At JS Auto, we employ a variety of testing methods and advanced equipment to thoroughly analyze and inspect the quality of iron castings. Each method is carefully selected to address specific aspects of quality, ensuring a comprehensive evaluation of the castings. These methods include:
Chemical Analysis
Chemical analysis is utilized to determine the precise composition of iron castings. Each element in the metal is tested to ensure that it meets the material standards. This analysis is critical because the chemical composition directly affects the material’s properties, such as its strength, ductility, and resistance to corrosion. If the test results conform to these standards, the castings receive a green light for quality. Accurate chemical analysis helps prevent failures and ensures that the castings will perform as expected in their intended applications.
Mechanical Testing
Mechanical testing verifies the metal properties of iron castings, assessing characteristics such as hardness, tensile strength, casting quality, and structural load capacity. This testing is essential to confirm that the castings can withstand the mechanical stresses they will encounter in service. By determining properties like yield strength and elongation, mechanical testing ensures that the castings meet the specified mechanical requirements, providing reliability and durability in their application.
Dimension Testing
Dimension testing guarantees that iron castings meet precise dimensional specifications. Ensuring that the physical dimensions of each casting align with design requirements is crucial for their integration into larger assemblies. Equipment such as Coordinate Measuring Machines (CMM) with tracing probes, contour profile tracers, and height gauges are used to verify that the dimensions align with client requirements. Accurate dimension testing prevents issues related to improper fit, which can lead to functional failures and increased wear.
Optical Testing
Optical testing, employing metallurgical microscopes with image analyzers, allows for the rapid and efficient inspection of metallographic materials. This equipment provides high-quality images and reliable results, facilitating quick and accurate metallurgical analysis. Optical testing can reveal details about the grain structure, phase distribution, and the presence of inclusions or defects within the material, all of which are critical for understanding the material's performance characteristics.
Non-Destructive Testing (NDT)
Non-Destructive Testing methods, including radar check meters, 3D scanning, endoscopy, and videocopy, assess the quality of castings without causing any damage. NDT techniques are crucial for detecting internal and surface defects that are not visible to the naked eye. These methods ensure the integrity and reliability of the castings while maintaining their usability. NDT allows for continuous monitoring and quality assurance throughout the production process, helping to prevent costly failures and ensuring that only defect-free components are delivered.
Quality Testing and Analysis at JS Auto
JS AutoCast is equipped with extensive in-house testing capabilities and state-of-the-art equipment for quality testing and analysis. Our facilities are designed to support a wide range of testing procedures, ensuring that every aspect of the casting process is monitored and controlled. By leveraging the latest and most robust technology, JS Auto consistently delivers excellence in the iron casting industry.
Our commitment to quality extends beyond mere compliance with standards; it is about continuous improvement and innovation. We invest in the latest technology and training for our staff to ensure that our testing methods are at the forefront of industry advancements. This dedication to quality ensures that our clients receive components that are not only fit for purpose but also exhibit superior performance and longevity. Ensuring that every product meets the highest standards of quality and precision is not just a goal but a core value at JS Auto. This approach has earned us a reputation for reliability and excellence in the iron casting industry, making us a trusted partner for our clients worldwide.