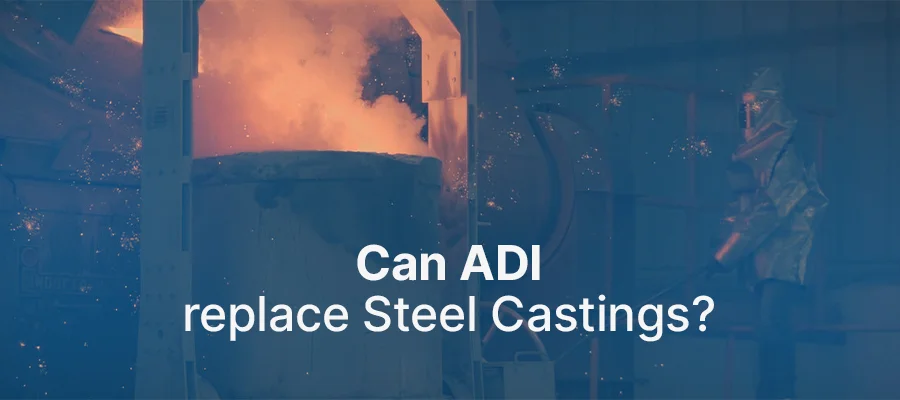
Can ADI replace Steel Castings?
August 16,2023
This question can be answered when we compare the properties of ADI and Steel w.r.t Manufacturing ease, cost competitiveness, machining ease and energy consumption. Some of the parameters in which ADI Castings score higher than Steel are mentioned below:
- Steel is far more difficult to cast than ADI.
- ADI has less stringent draft requirements than steel forgings.
- At temperatures below zero, ADI maintains more of its toughness than steel.
- Stress makes ADI work harder. ADI has more dampening capacity than steel.
- Due to ADI's lower casting temperature than steel, it is possible to cast complex shapes with sectional changes and achieve a superior surface finish.
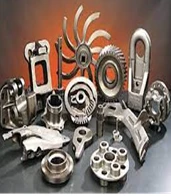
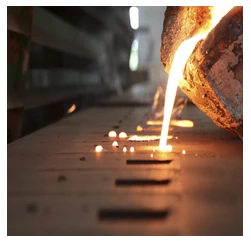
The Advantages in terms of Cost
Although the cost of ADI material is less expensive per kilogram than that of steel or aluminum, this only represents a small portion of the potential cost savings because an ADI-designed component can result in cost reductions at every stage of production. The cost to create ADI counterparts can then be half as much as that of an aluminum item or less than that of a steel forging. Value engineering benefits from ADI in number of ways:
- Excellent castability: Ductile iron has a very high yield rate, or the ratio of metal poured to metal supplied, and is easily cast into complex shapes.
- Lower machining costs: ADI is well suited to casting in close to net shape because it requires less metal to be removed from the starting material. Ductile iron has better machinability than free-machining steels before austempering. The cost per kilo is further decreased by the dense, manageable chips that ductile iron and ADI both create.
- Savings on heat treatment: Austempering delivers a higher level of homogeneity and predictable dimensional changes than carburising or induction hardening while generally costing less.
- Low energy content: ADI castings typically require 80% less energy to produce than steel forgings and 50% less energy than steel castings to create.
- Best price: ADI is typically the best deal when considering relative cost per unit of yield strength.
Advantages in terms of performance
Due to their better performance, ADI castings are swiftly supplanting steel forgings, welded fabrications, carburized steel, and aluminum in important applications.
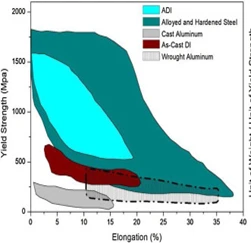
- Steel-equivalent strength
Due to ductile iron's equal strength, almost 80% of all cast and forged steels may be swapped out for a different grade of ADI. - Less dense than steel
ADI's relative weight per unit of strength allows for cost-effective design without sacrificing performance. An ADI component will weigh 10% less than steel for a particular shape. - 'Lighter' than aluminum
ADI weighs only 2.5 times as much and is three times stronger than the best cast or forged aluminum. A correctly constructed ADI part can replace aluminum while saving weight because it is twice as rigid. - Excellent fatigue strength ADI's dynamic characteristics are superior to those of forged, cast, and micro-alloyed steels, giving it excellent fatigue strength. In contrast to aluminum, ADI's endurance limit is steady after tens of millions of cycles.
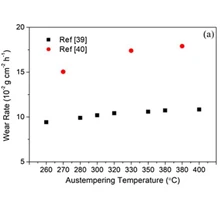
Superior wear and abrasion resistance
At lower "bulk" hardness levels, ADI exhibits greater abrasion resistance than commonly treated steels and irons. ADI improves with service, in contrast to carburized steel, which loses wear resistance as the carburized coating is gone. Its greater wear resistance versus steel at any given hardness level makes it the best material for applications requiring intense abrasion, such as earth moving.